Flanged butterfly valves and groove butterfly valves are two popular types of butterfly valves. While they share some similarities, there are some key differences between them. For example, they have different designs, installation methods and applications. Here is a detailed comparison:
1. Design and Connection of Flanged Groove Butterfly Valve
* Flanged Butterfly Valves
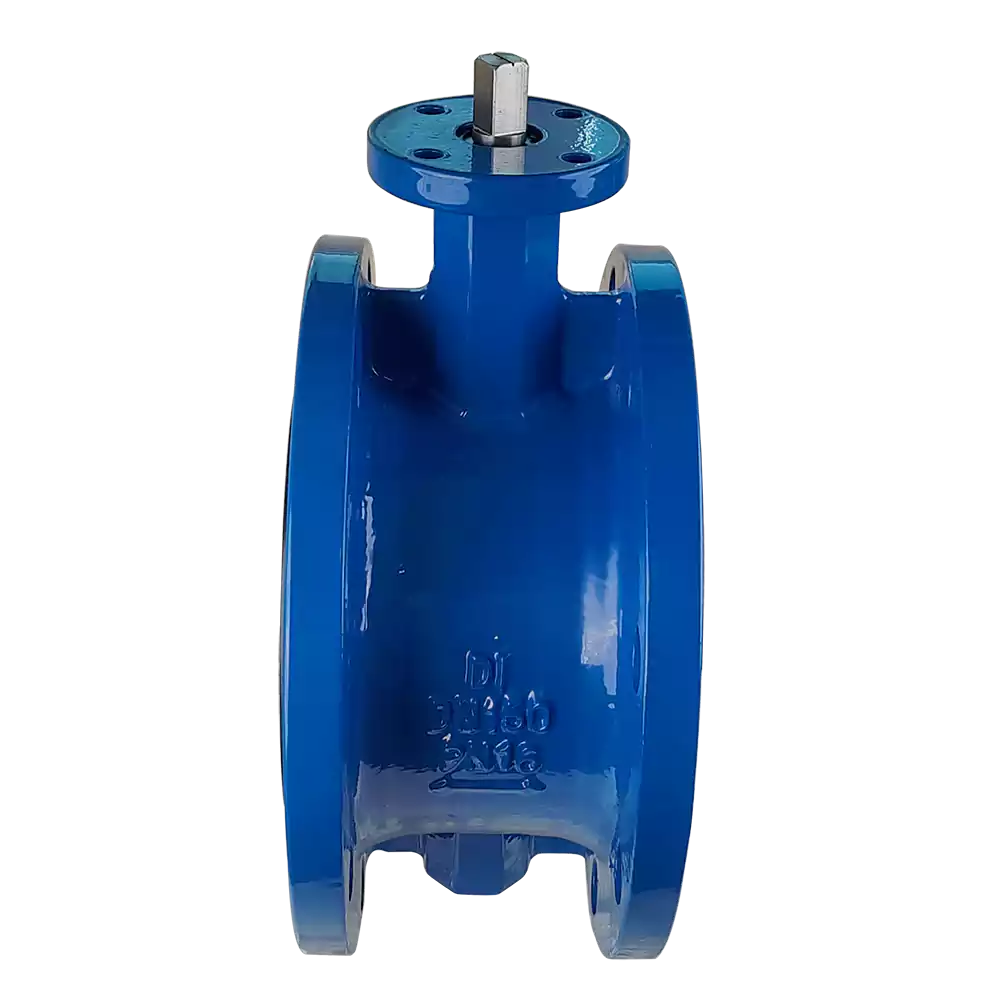
– Flange butterfly valve has a metal flange on each side of the valve body, which is directly bolted and easily connected to the flange fixed on the pipe flange.
– Structure: The more common type is centerline butterfly valve, of course, double eccentric and triple eccentric butterfly valves are also commonly used.
– Standard: usually follow ANSI, DIN or JIS flange standard.
– Sealing: soft seal comes with rubber seat sealing, which can be directly connected to the pipe flange, while hard seal butterfly valves achieve sealing through the gasket placed between the valve flange and the pipe flange.
* Grooved Butterfly Valve
– The grooved butterfly valve is a standardized groove that is recessed inward at the end of both sides. This is where it gets its name. The grooves are used for mounting to mechanical fittings or clamps.
– CONSTRUCTION: Centerline butterfly valve only.
– Standard: Usually follow ANSI, DIN or ISO standard.
– Seal: Usually made of stainless steel or cast iron with built-in rubber seal for quick connection and sealing.
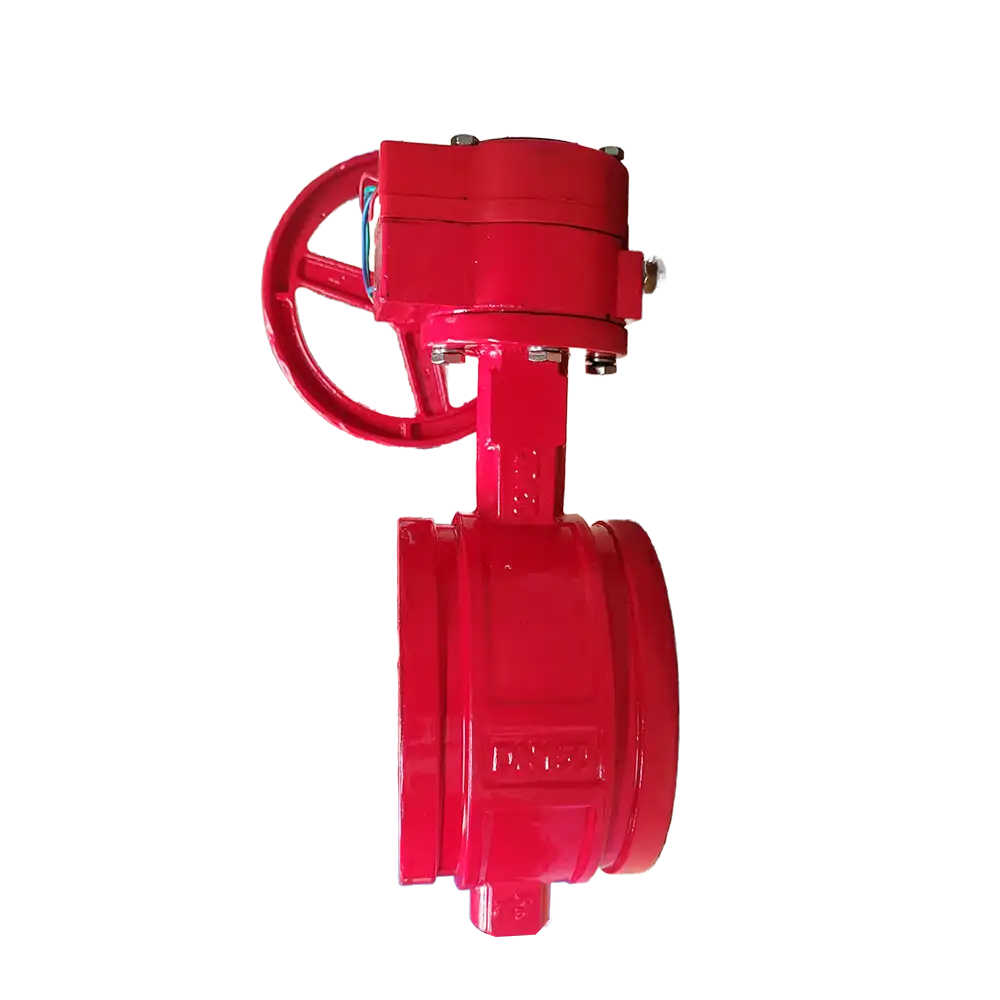
2. Installation and maintenance of Flanged Groove Butterfly Valve
*Flange Butterfly Valves
– Installation: requires precise alignment of the flange and proper tightening of the bolts.
– Maintenance: Time-consuming disassembly due to bolting.
– Space: Takes up more space due to flange thickness and bolting.
*Grooved Butterfly Valve
– Installation: Faster and easier to install with mechanical joints.
– Maintenance: Quick and easy to disassemble for inspection or maintenance.
– Space: shorter structure length compared to flanged butterfly valve.
3. Pressure and temperature ratings
*Flanged butterfly valves
– Pressure Range: Typically capable of handling higher pressures, eccentric butterfly valves can withstand up to PN25 or higher, depending on construction and material design.
– Temperature: Can withstand higher temperatures due to the provision of metal seats.
*Grooved Butterfly Valves
– Pressure range: Suitable for lower pressure systems, typically no higher than PN16 Temperature: Due to the need for the valve plate to be encapsulated.
– Temperature: Limited temperature range due to the need to overmold the valve plate and the use of rubber gaskets.
4. Applications
*Flanged Butterfly Valves
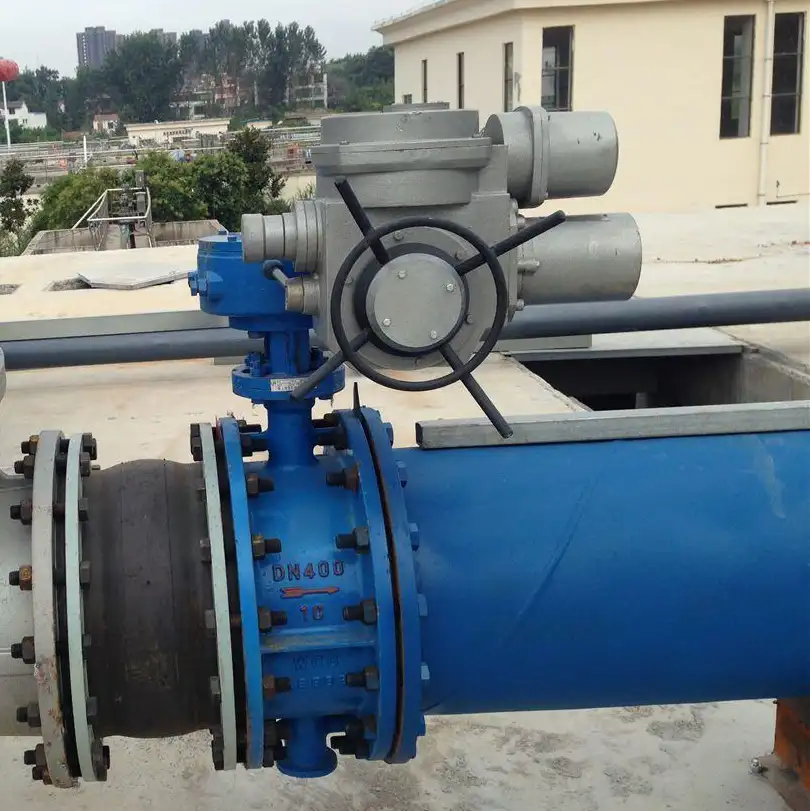
– Wide range of applications: Suitable for industrial applications with low, medium or higher pressure and temperature ratings.
– Industries: chemical plants, oil and gas, power generation, water treatment and marine systems.
* Grooved Butterfly Valve
– Light to medium duty: For systems with moderate pressure and temperature requirements.
– Industries: HVAC systems, fire protection systems and water supply networks.
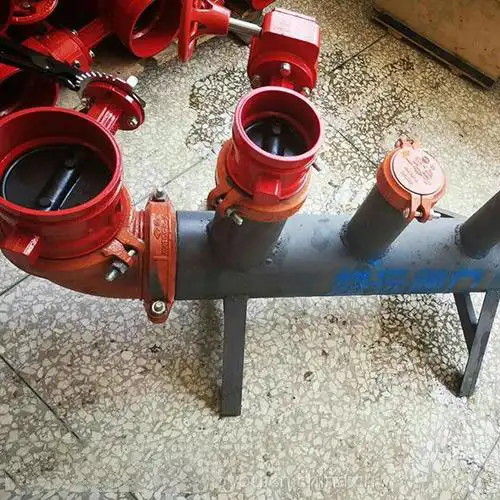
5. Cost
*Flanged Butterfly Valves
– Initial Cost: Higher due to the need for flanges and bolting material.
– Installation cost: Increased due to labor-intensive installation.
*Grooved Butterfly Valve
– Initial cost: Usually lower than flanged valves.
– Installation Cost: Lower cost due to quick and easy installation.
6. Advantages and limitations
*Flanged Butterfly Valves
– Advantages: High durability for extreme conditions. Limitations: Requires more space, heavier, longer installation time.
– Limitations: more space required, heavier, longer installation time.
*Grooved butterfly valve
– Advantages: light weight, easy to install and maintain, compact design.
– Limitations: Limited to moderate pressures and temperatures, dependent on coupling integrity.
Choose flanged butterfly valves for demanding industrial environments or grooved butterfly valves for systems requiring quick installation and moderate performance.