PTFE-lined butterfly valves offer a durable seal with full chemical resistance. This means that even highly aggressive and corrosive media can be safely routed.
1. Features of PTFE Lined butterfly valve
1.1 PTFE lined butterfly valve has simple construction, small size, lighter weight, raw material loss province, small, fast power switch, 90 ° reciprocating rotation, driver torque is small, etc.. It is used to disconnect, access, adjust the pipeline in the substance. it has excellent liquid manipulation characteristics and closing sealing characteristics.
1.2. PTFE butterfly valve can transport sand slurry, in the pipe hole hoarding liquid body at least. Under the bottom pressure, it can accomplish excellent sealing. Good adjustment characteristics.
1.3. The streamline design scheme of the butterfly plate makes the liquid friction resistance damage small, which can be regarded as an environmentally friendly commodity.
1.4. The valve seat for the through-rod structure, through the heat treatment, has excellent comprehensive physical properties and corrosion resistance, resistance to abrasion. PTFE butterfly valve open and close the valve seat only for rotating movement without lifter operation, the filler of the valve seat is not easy to destroy, sealing dependable. Fixed with the cone pin of the butterfly plate, the outreach end of the anti-breakage type design program to prevent accidental cracking in the valve seat and the butterfly plate at the interface when the valve seat crashed out.
1.5. Interface with live flange, clamping coupling, butt welding coupling and lug clamping coupling.
Tianjin Zhongfa Valve is a professional butterfly valve manufacturer, PTFE butterfly valve is one of our main products. ZFA has one-piece PTFE butterfly valve, split PTFE butterfly valve, fully lined PTFE butterfly valve, and half lined PTFE butterfly valve etc,.
2. Charactoristics of Split PTFE butterfly valve
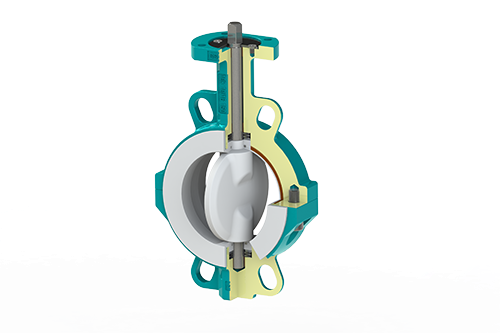
- Size range: 2″ – 12″ (DN 50 – 600)
- Temperature range: -20°C ~ 180°C
- Working Pressure: Max 150 Psi (10 bar)
- Leakage rating: Bi-directional bubble class seal
- Valve body material: cast iron, ductile iron
- Valve seat material: PTFE, RPTFE
- Valve plate material: CS+PTFE, SS+PTFE
- Valve stem material: SS420, 17-4PH
- Design standard: API 609
- Test standard: API 598
- Flange Standard: ASME B16.5 Class 150, EN 1092 PN10, PN16, JIS B2238 10K
- Upper flange standard: ISO5211
- Product application: highly corrosive, toxic media, acid, alkali, ultrapure water
3. Component Composition of PTFE Butterfly Valve
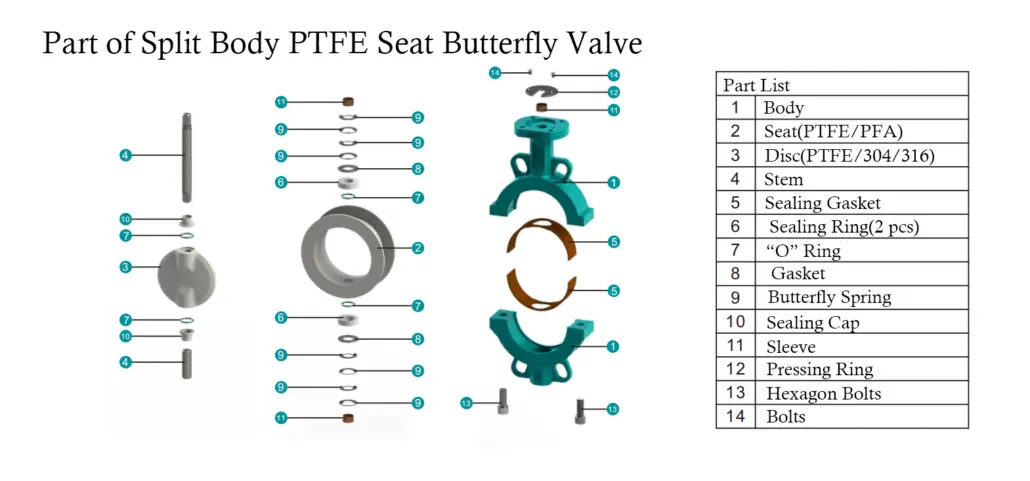
4. Product Features of Two Pieces Body PTFE Butterfly Valve
The valve body and butterfly plate lined with PTFE, PFA and other fluoroplastics, blocking direct contact with the medium, have unparalleled resistance to corrosion, infiltration and microbial contamination, with minimal maintenance to obtain higher purity and reliability.
Multiple axial sealing systems consisting of elastic disc springs and other components ensure the product’s reliable performance, thus realizing long-term maintenance-free operation.
Precision-machined PTFE valve seats and butterfly plates on CNC lathes ensure an effective fit and lower operating torque for longer service life.
Streamlined butterfly plate design to provide greater flow requirements.
High strength alloy steel material spindle protects the overall performance of the valve.
5. Product Features of ZFA Split Body PTFE Butterfly Valve
ZFA’S stem axial multiple sealing system Designed for reliable, maintenance-free service, Zhongfa’s three-step stem sealing system provides unrivaled sealing for long-term, zero-leakage performance.
5.1 The primary seal transmits preloaded pressure to the spherically curved surface of the lined valve plate nose via resilient disc springs;
5.2 The secondary seal incorporates resilient PTFE sealing rings in grooves machined in the upper and lower hubs of the valve plate, which are encapsulated in pure PTFE on the seat surface.
The sealing ring is covered by pure PTFE material on the surface of the valve seat, when the valve assembly process, it is compressed and squeezed by the valve plate and seat during the valve assembly process, which generates upward and downward pressure on the surface of the valve plate and seat, thus playing a sealing;
5.3 Three-stage sealing in the middle of the valve stem using pressure blocks and O-ring sealing fit, through the elastic disc spring and valve assembly process of extrusion.
By the elastic disc spring and the valve assembly process of extrusion, to the axial transmission of pre-pressure, so that the O-ring sealing ring pumping tight seat protruding lining layer.
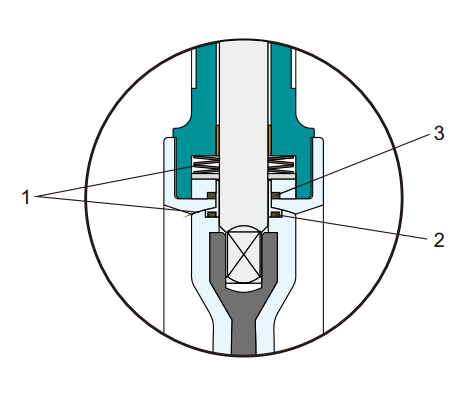