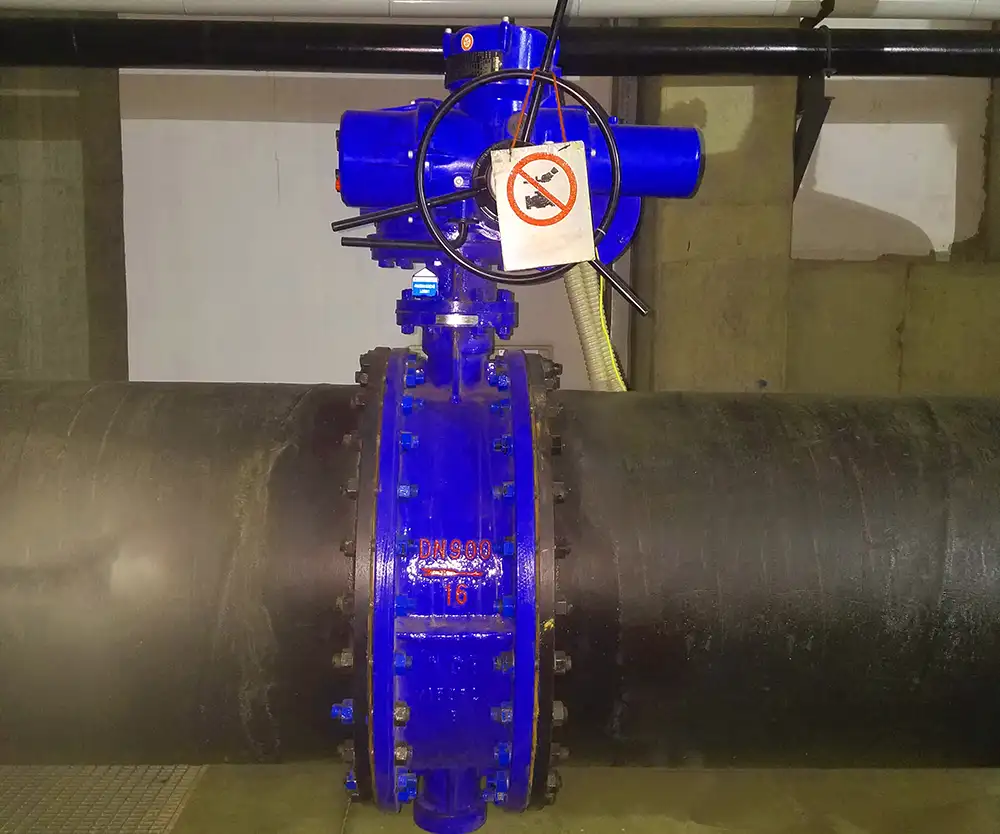
Brief introduction
Butterfly valve is an important valve type for fluid control. In the selection process, the correct selection of valve size is crucial because it directly affects the performance, safety and economy of the system. Let us discuss the applicable occasions and the key points of butterfly valve size selection.
1. Key Butterfly Valve Dimensions
When measuring a butterfly valve, several dimensions are critical:
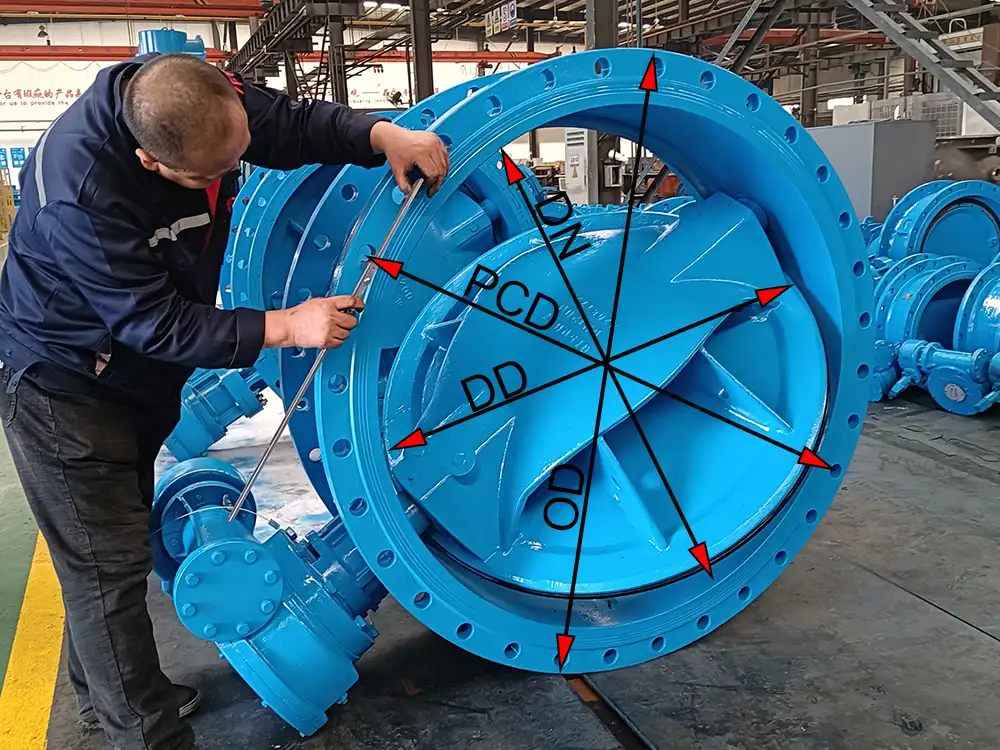
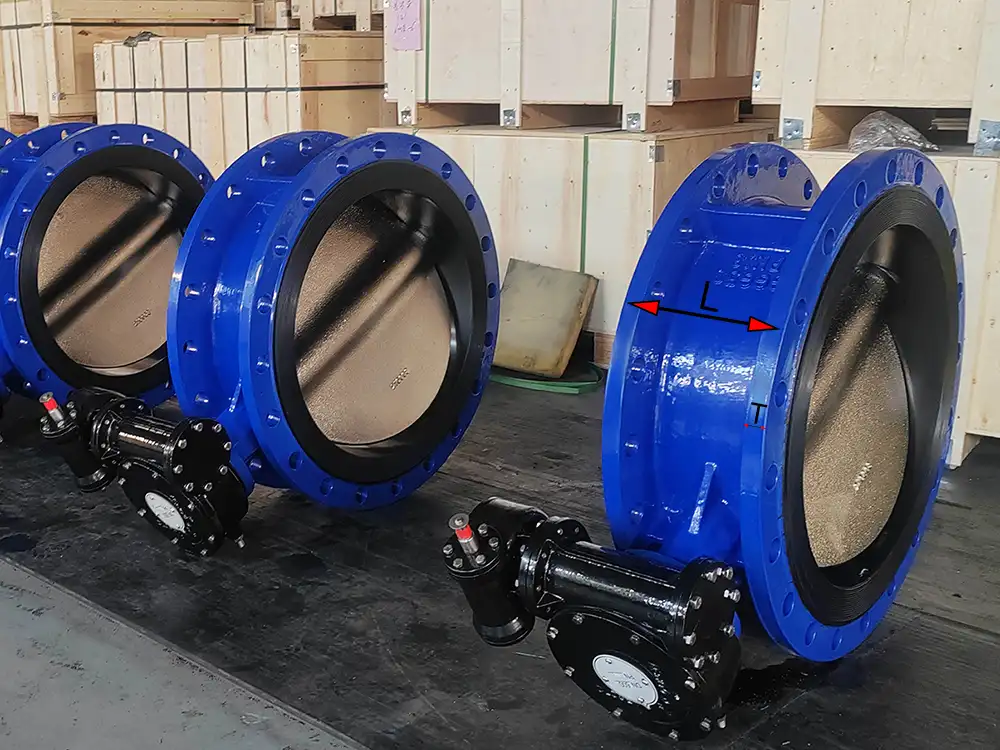
1.1 Nominal Diameter (DN):
This refers to the inside diameter of the valve. Usually measured in millimeters (mm) or inches (in).
1.2 Face-to-face dimension (L):
The distance between the two faces of the valve. This dimension is standardized and is critical to whether it can be installed in the pipeline.
1.3 Outside Diameter (OD):
The outside diameter of the valve body.
1.4 Bolt Circle Diameter (BCD):
The diameter of the circle through the center of the bolt holes in the flange.
1.5 Number and size of bolt holes:
Specifies how many bolts are required and their sizes.
1.6 Disc Diameter(DD):
The diameter of the disc inside the valve.
1.7 Shaft Diameter (SD):
The diameter of the shaft that holds the disc. The header size is important for the shaft and is related to whether it can be installed and driven.
1.8 Thickness (T):
The thickness of the valve body (known by measuring the thickness of the flange).
2. Standards of the butterfly valve dimension
Butterfly valves are manufactured to various international standards that specify dimensions, materials, and testing procedures.
Some common standards include:
2.1 ISO (International Organization for Standardization):
ISO 5752 specifies face-to-face and center-to-face dimensions.
2.2 ANSI (American National Standards Institute):
ANSI B16.1 for cast iron flanges and flange fittings.
2.3 API (American Petroleum Institute):
API 609 specifies general and special purpose butterfly valves.
2.4 EN (European Standard):
EN 593 applies to industrial butterfly valves and is the most common standard. If there is no special requirement, we generally use this standard.
3. Why the dimension is important
3.1 Pipe System Flow Needs
3.2 Pipe Pressure
3.3 Flow Rate of Medium
4. Tools and equipment for measuring
To measure butterfly valves accurately, you need the following tools. After all, “the best tool is the best tool. A workman must first sharpen his tools if he is to do his work well”:
• Caliper: used to measure diameter and thickness.
• Box ruler: used to measure larger dimensions such as face-to-face length.
• Vernier ruler: used to accurately measure small parts.
• Micrometer: used to measure small and precise dimensions.
5. Measuring Guide
Many dimensions are measured after processing and before assembly. The measurement after assembly is for secondary confirmation.
5.1. Measuring the nominal diameter (DN)
Use a caliper to measure the inner diameter of the valve body. Place the caliper inside the valve body and extend it to the contact sides. (Use a box ruler for large diameters) Note that it must pass through the center of the valve body to measure accurately.
5.2. Measuring the FTF face-to-face dimension (L)
Use a tape measure to measure the distance between the two faces of the valve.
5.3. Measuring the outside diameter (OD)
Same as measuring the nominal diameter DN.
5.4. Measuring Bolt Circle Diameter (BCD) and Bolt Hole Size
Use a caliper to measure the distance from the center of one bolt hole to the center of the opposite bolt hole (across diameter). Alternatively, use a gauge to measure the diameter of a single bolt hole.
5.5. Measuring Disc Diameter, Shaft Diameter and Shaft Head Size
Use a caliper to measure the disc diameter. For the shaft, measure its diameter where it connects to the disc.
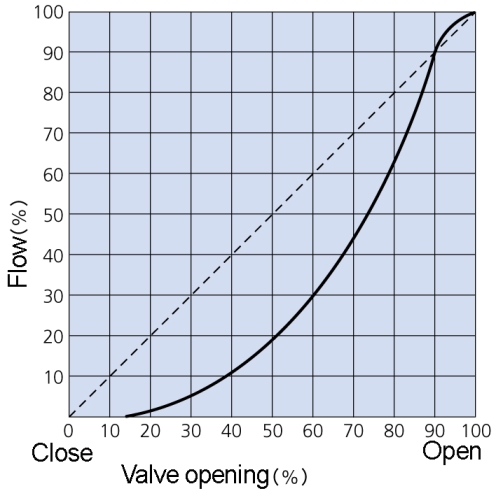
6. Type selection of butterfly valves

7. Safety
8. Fluency of Opening and Closing
- As can be seen from the above, a small-sized butterfly valve will cause the pressure to increase, which means that the pressure on the butterfly plate will also increase, the torque will increase, and the output torque of the actuator will also increase. If the output torque of the actuator is less than the closing torque of the butterfly valve, the butterfly valve will not close.
- If the size of the butterfly valve is too small, it will also cause the butterfly valve to get stuck.
9. Manufacturing Cost
10. Applications
Understanding and accurately measuring butterfly valve dimensions is critical for a variety of applications:
• Pipeline design: Ensure the valve fits properly in the pipeline and meets flow requirements.
• Maintenance and repair: Facilitate replacement of parts and maintain system integrity.
• Quality control: Ensure that the valve meets the required specifications and standards during manufacturing.
11. Case Studies and Examples
11.1. Industrial Applications
Case Study: A water utility needed to replace several butterfly valves in its piping system. Accurate measurements were critical to ensure the new valves fit and operate efficiently.
Solution: By following the measurement steps above, the water utility maintenance team successfully measured the required dimensions. The new valves are installed with minimal downtime and are perfectly fitted into the piping system.
11.2. Manufacturing Quality Control
Case Study: ZFA valve manufacturer needs to ensure that butterfly valves meet international standards before shipment.
Solution: ZFA or a third-party inspection agency (customer-commissioned) implements a strict measurement protocol using a variety of measuring tools. This ensures that all butterfly valves meet the specified dimensions and quality standards.
12. Conclusion
Accurately measuring the dimensions of butterfly valves is important, especially to ensure correct installation, function and compliance with industry standards.
The process involves:
12.1. Measuring key dimensions:
nominal diameter, structural length, outer diameter, bolt circle diameter, number and size of bolt holes, valve plate diameter, shaft diameter and shaft head size and valve body thickness.
12.2. Using appropriate tools and techniques:
calipers, box gauges, vernier rulers, micrometers and ultrasonic thickness measurement.
12.3. Complying with international standards: ISO, ANSI, API, EN.
By mastering these aspects, you can ensure reliable performance and service life of butterfly valves in various applications.